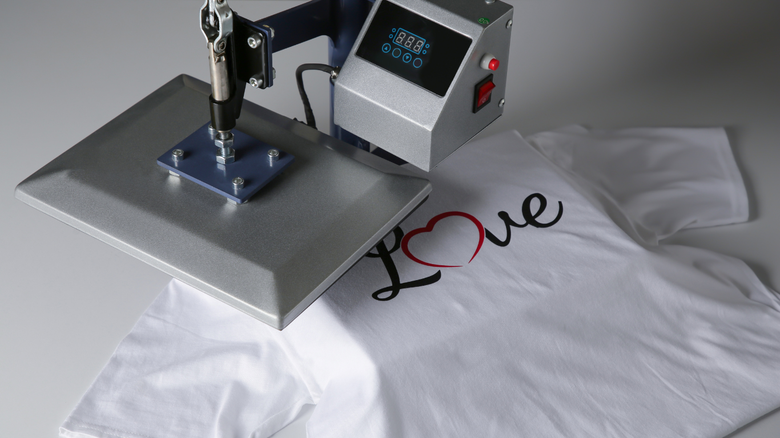
Do you want to make your own personalized t-shirts, tote bags, or other fabric projects? If so, you might want to try using heat transfer vinyl, also known as iron-on vinyl. Heat transfer vinyl is a special type of vinyl that can be cut with a cutting machine, such as a Cricut, Silhouette, Loklik, etc., and then, transferred to fabric using heat. It is a fun and easy way to create custom designs that last for a long time.
In this blog post, I will show you how to use heat transfer vinyl in five simple steps. A video is available at the end of this post.
You will need the following materials and tools:
• Heat transfer vinyl (I recommend HTVRONT, Siser Easyweed HTV or Cricut Iron-On Vinyl)
• A blank fabric item, such as a t-shirt, a tote bag, a pillowcase, etc.
• A cutting machine, such as Cricut or Loklik
• A standard grip mat
• A weeding tool
• A heat source, such as an iron, a Cricut EasyPress, or a heat press
• A heat-resistant surface, such as an EasyPress mat or a folded towel
Step 1: Create or upload your design
The first step is to create or upload your design in the cutting machine software that you are using. You can use any image or text that you want, as long as it is compatible with your software. For example, if you are using Cricut Design Space, you can use SVG, PNG, JPG, or DXF files. If you are using Silhouette Studio, you can use SVG, PNG, JPG, or STUDIO files. With LOKLIK, you can use SVG, PNG, or JPG files.
You can also use the built-in shapes, fonts, and images in your software, or browse online for free or paid designs. I usually design my own by either drawing or painting them, or I use Canva, Cricut Design Space, or the Loklik IdeaStudio. However, if you're not into drawing or designing your own, you can find some really cool pre-made designs at designbundles.net. You can purchase designs, sign up for their monthly subscription, or choose from their selection of free designs.
Once you have your design ready, make sure to resize it to fit your fabric item. You can use the grid and the rulers in your software to measure the dimensions of your design. You can also use a tape measure or a ruler to measure the actual size of your fabric item and adjust your design accordingly.
One important thing to remember when using heat transfer vinyl is that you need to mirror your design before cutting. This means that you need to flip your design horizontally so that it looks reversed on the screen. This is because you will be cutting the vinyl on the back side and then flipping it over to apply it to the fabric. If you don't mirror your design, it will end up backwards on your fabric item.
To mirror your design in Cricut Design Space, select your design and click on the Flip button on the top toolbar. Then choose Flip Horizontal. To mirror your design in Silhouette Studio, select your design and click on the Replicate button on the right toolbar. Then choose Mirror Right. To mirror your design in LOKLIK IdeaStudio, one the cut screen, it will have the mirror option on the bottom left of the prompt box.
Step 2: Cut your design
The next step is to cut your design with your cutting machine. To do this, you need to place your heat transfer vinyl on your cutting mat with the shiny side facing down. The shiny side is the carrier sheet, which is a clear plastic layer that holds your vinyl in place and protects it from the heat. The dull side is the actual vinyl, which is the side that you want to cut.
Make sure to smooth out any wrinkles or bubbles on your vinyl and align it with the grid on your mat. I like to use a brayer or a squeegee Then load your mat into your cutting machine and follow the instructions on your software to select the material type, the blade settings, and the cut pressure. For example, if you are using Cricut Design Space, you can choose Iron-On as the material type and set the Fine-Point Blade as the blade type. If you are using Silhouette Studio, you can choose Heat Transfer Material as the material type and set the AutoBlade as the blade type. The LOKLIK is pretty simple. When choosing the material, it will state which blade to use, you can then insert the blade that it suggests, but with most vinyl, you use the standard blade. It's only going to recommend a different blade for thicker materials, such as cardstock or leather.
Then click on the Cut button on your software and wait for your machine to finish cutting your design. Once it is done, unload your mat and peel off the excess vinyl around your design. This is called weeding, and you can use a weeding tool to help you remove the unwanted parts of the vinyl.
Step 3: Prep your fabric item
The third step is to prep your fabric item for the heat transfer. To do this, you need to preheat your fabric item with your heat source for a few seconds. This will help to remove any wrinkles or moisture from your fabric and make the vinyl adhere better.
You also need to place your fabric item on a heat-resistant surface, such as an EasyPress mat or a folded towel. This will protect your work surface from the heat and provide a firm and even base for the heat transfer.
Step 4: Apply your design
The fourth step is to apply your design to your fabric item using heat. To do this, you need to position your design on your fabric item with the carrier sheet facing up and the vinyl facing down. Make sure to align your design where you want it to be and check for any spelling or placement errors.
Then cover your design with a teflon sheet, or parchment paper will work if you don't have a teflon sheet. Some vinyl bundles will come with a sheet. They are reusable, therefore, environmentally friendly. This will protect your heat press or iron in case the carrier sheet melts. However, the carrier sheet shouldn't melt, and most of the time, you can iron directly over it without any sheet. I just like to use one just in case.
Next, press your design with your heat source for the recommended time and temperature settings. You can check the manufacturer's website or the packaging of your vinyl for the specific instructions. For example, if you are using Siser Easyweed HTV and a Cricut EasyPress, you can set the temperature to 305°F and the time to 15 seconds. If you are using an iron, you can set it to the cotton setting and press firmly for 25 to 30 seconds. Make sure the steam setting is turned off. If you can't turn off the steam, as is with my iron, you will need to empty all the water out of your iron. I usually hit the sprayer until all the water is gone. This is a tedious and time consuming task, but if it's the only heat source you have, and you really want to iron on your design, it is doable.
Make sure to apply even pressure and move your heat source slightly over your design to cover the entire area. You can also flip your fabric item over and press from the back side for another 10 to 15 seconds for extra durability.
Step 5: Peel off the carrier sheet
The final step is to peel off the carrier sheet from your design. Depending on the type of vinyl you are using, you can either peel it off when it is hot, warm, or cold. This is called the peel type, and you can check the manufacturer's website or the packaging of your vinyl for the specific instructions. For example, if you are using Siser Easyweed HTV, you can peel it off when it is hot or warm. If you are using Cricut Iron-On Vinyl, you can peel it off when it is cold. If your vinyl is cool peel, you can lay your item, face down, on a cool counter, and it will cool off faster than it would if you just leave it on your pressing mat.
To peel off the carrier sheet, start from one corner and slowly peel it back at a 45-degree angle. If it's hot peel, be careful not to burn your fingers or pull too hard on the vinyl. If you notice that some parts of the vinyl are not sticking to the fabric, you can cover them with the cloth again and press them with more heat and pressure. This sometimes happens, so I suggest always peeling slowly with one hand, while using your other hand to press down on the fabric near the carrier sheet, moving your hand along the shirt as you peel. This will keep the shirt flat and keep it from rising up as you peel. Be sure to pay attention to the vinyl to make sure it's not lifting as you remove the carrier sheet. This way you can easily lay the carrier sheet back down so you can re-press.
And that's it! You have successfully used heat transfer vinyl to create your own custom fabric item. You can now enjoy your new creation or give it as a gift to someone special. Just remember to follow the care instructions for your vinyl and your fabric item to make them last longer. Usually, this means to wash them inside out in cold water and tumble dry on low heat or air dry. You can read our post, How to Prolong the Life of Your T-shirt for more tips on washing your item. Each of our shirts also come with a care instructions card.
I hope you enjoyed this blog post and learned how to use heat transfer vinyl. If you have any questions or comments, feel free to leave them below. Happy crafting!
DISCLAIMER: As an Amazon Associate, we will earn a small commission, at no extra cost to you, if you make a purchase through the links on our blog. We are not employees of Amazon. We just love shopping at Amazon and sharing our favorite products. We appreciate any and all purchases made through our links, as they allow us to keep making stuff so we can keep sharing it with you! Thanks for your support!❤️❤️❤️
Sam's Signature YouTube Channel video "How to Add HTV to a T-shirt | Using My Loklik Cutter
Add comment
Comments